Forthcoming Articles
International Journal of Automotive Composites
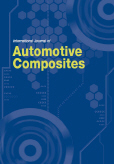
There are currently no forthcoming papers for this journal.
Register for our alerting service, which notifies you by email when new issues are published online.
There are currently no forthcoming papers for this journal.
Register for our alerting service, which notifies you by email when new issues are published online.